五軸高速加工中心是復雜零件精密加工的利器,其加工效率受設備性能、工藝規(guī)劃與操作精細程度共同影響。通過科學調(diào)整和精確操作,可以在保持高精度的同時提升加工效率,減少資源浪費和生產(chǎn)周期。
??一、優(yōu)化工藝路徑,減少加工空行程??
加工效率的提升依賴于工藝路徑的優(yōu)化。在編程階段,要合理規(guī)劃刀具路徑,避免不必要的空移運動。多軸聯(lián)動加工時,可通過合理排序工序確保刀具持續(xù)有效切削,減少重復定位與無效動作。在五軸加工中,合理設計傾斜角度可減少刀長干涉,擴大可加工區(qū)域,從而減少工件的多次裝夾。
同時,仿真軟件的使用尤為關鍵。通過仿真功能可提前驗證數(shù)控程序的可行性,發(fā)現(xiàn)路徑錯誤或潛在干涉問題,減少試切時間。合理劃分加工區(qū)域的先后順序,利用五軸機床的運動性能,優(yōu)先處理淺層余量區(qū)域,能加快整體加工進程。
??二、強化刀具管理與切削參數(shù)設置??
刀具的狀態(tài)直接影響加工效率。操作中需確保刀具鋒利度,并根據(jù)工件材料選擇適當?shù)牡毒咝吞柵c涂層。加工過程中,密切關注刀具磨損并及時更換,避免因磨損加劇導致的加工質量下降和停機調(diào)整。
在保證加工質量的前提下,適當提升切削參數(shù)。這種優(yōu)化需結合設備性能與刀具材質特性,使主軸在高效運行狀態(tài)下穩(wěn)定工作。同時,在五軸聯(lián)動加工中,刀軸的控制需要更加精確,避免因頻繁調(diào)整角度而影響加工流暢性。
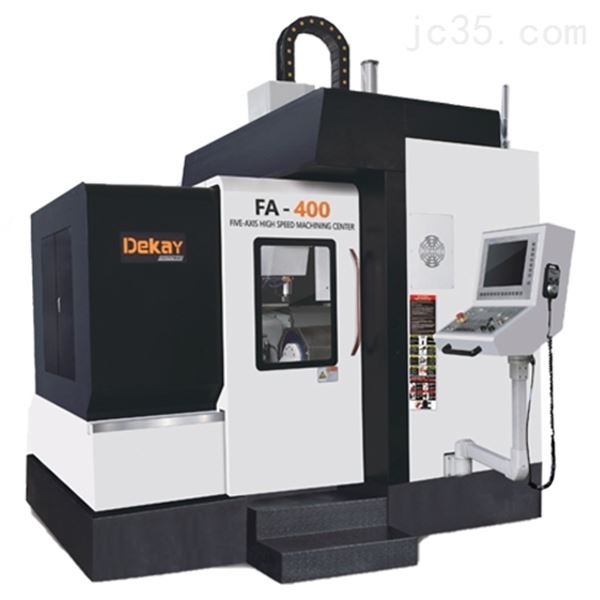
??三、提升人員操作水平與設備監(jiān)控??
五軸加工需要精細操作與合理調(diào)度。操作人員需熟記機床性能特點,熟練掌握工藝系統(tǒng)各環(huán)節(jié)配合,靈活調(diào)整工裝夾具及輔助裝置,避免因調(diào)試浪費時間。對復雜工件,可通過局部加工與仿真檢測交替進行,減少返修帶來的時間損失。
此外,精細化管理設備運行狀態(tài)至關重要。及時檢查冷卻系統(tǒng)、潤滑系統(tǒng)和傳動部件,確保設備運行無異常,降低停機風險。五軸加工機床中,伺服和傳動系統(tǒng)的高效運作直接影響加工流程,對設備進行周期性校核與維護,保證運動精度與速度始終處于較佳狀態(tài)。
??四、利用數(shù)字化技術簡化流程??
五軸高速加工中心通常配有數(shù)字化接口,可對接生產(chǎn)管理軟件。借助編程仿真與自動換刀功能,可快速切換加工任務,減少人工調(diào)整工序時間。通過高效整合多工藝需求,將設備利用率更大化。
精密操作的每個環(huán)節(jié)均與加工效率密切相關。通過優(yōu)化工藝路徑、管理刀具使用、細化設備控制及利用數(shù)字化技術,可有效提升五軸高速加工中心的運行速度,同時確保加工質量和生產(chǎn)安全。